Filter by
Sort
Sub-category
- Body Parts (1)
- Chemicals (56)
- Construction (140)
- Construction and Heavy Equipment (68)
- Crane and Rigging (19)
- Driver Awareness (25)
- Driver and Transportation Safety (34)
- Drug and Alcohol Policies (2)
- EHS Awareness (1)
- EHS Manager (45)
- Electrical and LOTO (22)
- Employment Liability (23)
- Environmental (41)
- Ergonomics (18)
- Ergonomics and Office Safety (23)
- Fire Extinguisher (24)
- Fire Safety (7)
- First Aid (18)
- Food Services and Distribution Safety (52)
- General Safety (140)
- General Safety and Manufacturing (479)
- General Safety and Manufacturing: Fire Safety (9)
- HR Employment Liability (2)
- Hazmat (4)
- Health and Safety Management (75)
- Health and Safety Management: Global (2)
- Health and Wellness (65)
- Healthcare (9)
- Hot Work (3)
- Laboratory Safety (63)
- Management Skills (20)
- Other (28)
- Pandemic (6)
- Prevention and Egress (5)
- Slips (24)
- Substances and Hazard Communication (57)
- Tools (23)
- Transportation Safety (32)
- Warehouse Safety (30)
- Wind Turbine (6)
- Workplace Safety (309)
Training Bundles
- Alcohol Awareness
- Artificial Intelligence
- Cybersecurity Essentials
- Digital Transformation
- Diversity, Equity & Inclusion
- DOT/CDL
- Drug Free Compliance
- Financial Compliance
- First Aid
- Food Safety
- HIPAA Compliance
- Leadership
- Mental Health & Wellbeing
- OSHA / Construction Safety
- Personal Development
- Project Management
- Retail
- Workplace Harassment
- Workplace Safety
Browse by State
Language
Browse by Tags
Browse by Price
Browse by Duration
Browse by Audience
Online Safety Courses
Courses
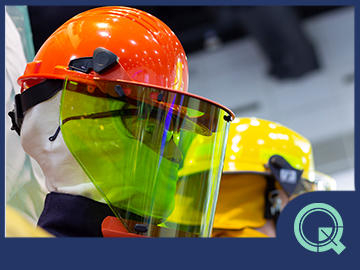
Safety
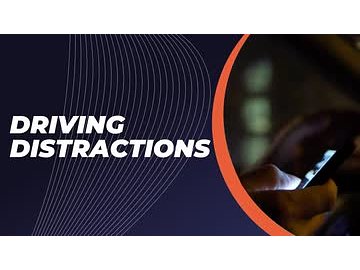
Safety
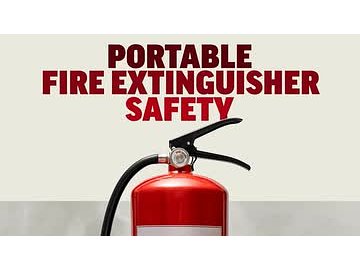
Safety
Portable Fire Extinguisher Safety
$4.95
193 views
by HSI - Health & Safety Institute
Subscribe to Prime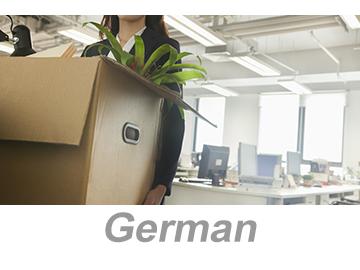
Safety
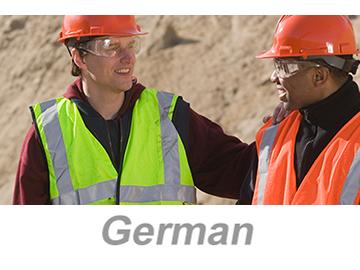
Safety
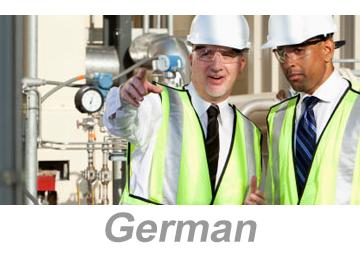
Safety
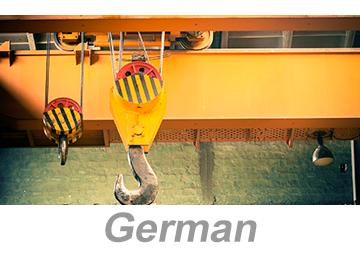
Safety
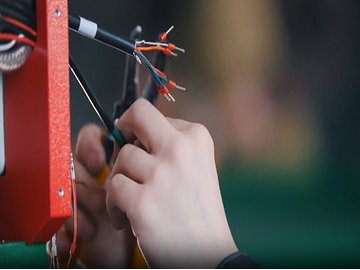
Safety
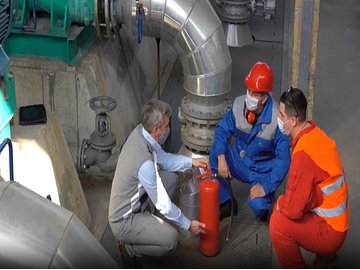
Safety
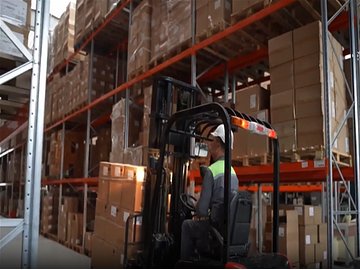
Safety
Online Safety Courses and Certifications: Get Trained, Get Ahead
With over 1,400 online safety training courses, we have become an industry leader that will help you meet your safety training needs. A cloud-based learning ecosystem, we bring a whole universe of online safety training programs. Our courses belong to a wide array of sub-categories, and we add new courses regularly to cater to the most diverse learning needs.
Our top sub-categories include construction, drug and alcohol policies, employment liability, food services and distribution safety, healthcare, general safety and manufacturing, health and wellness, pandemic preparedness, workplace safety, and more.
Unlike other safety training course providers, we ensure our course materials are prepared by leading learning designers and environmental and safety personnel. We take feedback from our learners regularly to make sure every course module’s content is up to date and easy to understand.
Better yet, you’ll take these safety training programs in not only English but also multiple languages, including Spanish, French, Thai, German, Portuguese, Italian, Arabic, and the like. Our programs are available for employees and supervisors. So, regardless of your professional background, we will have a course to cover your training needs.
We notice many e-learning portals pricing their training safety programs exorbitantly these days. But we are different in a good way. Our training safety programs are priced competitively so that monetary constraints do not stop personnel from improving their skill set. Since our coursework is available online, you can learn 24/7/365 from any device.
Enroll in one of our online safety training certifications today. That is how you will give safety learning the priority it deserves
If you still think safety is just a buzzword, think again. It's more than that; it's a way of life. And if you are a professional working in a high-risk industry, safety training and certification can make a significant difference.
What Is Safety Training And Certification?
Safety training and certification are essential components of safeguarding individuals and workplaces. Safety training educates and prepares individuals to prevent accidents, respond to emergencies, and adhere to industry-specific safety standards.
And safety professional certifications are tangible proof of your knowledge and skills in safety management. They can enhance your employability in industries where safety is a priority.
Why Choose Coggno For Safety Training And Certification?
Coggno is your one-stop destination for safety training and certification. We provide an extensive library of safety training courses, from basic safety guidelines to industry-specific compliance training. You can find the right course to suit your needs and career goals. Coggno's user-friendly platform makes online safety training accessible and convenient. You can learn at your own pace, whenever and wherever it suits you.
Furthermore, we offer accredited safety certificates recognized by industry leaders. These certificates can boost your credibility in the industry.
What Are The Advantages Of Coggno's Safety Training Certification?
-
Industry-Leading Instructors: Coggno's courses are developed and taught by industry experts who understand real-world challenges and requirements.
-
Customized Learning Paths: Tailor your learning to your unique needs, whether you're just starting or looking to specialize in a particular safety area.
-
Tracking and Reporting Capabilities: Coggno's platform allows you to track your progress and generate reports, providing a clear overview of your training and safety certifications.
How To Get Started With Safety Training And Certification
-
Selecting the Right Courses: Select the courses that align with your career objectives and industry standards. Coggno's platform simplifies this process, making it easy to find the perfect course.
-
Registration and Enrollment: Enrolling in safety training courses through Coggno is straightforward. Register, pay, and you're ready to start learning, all from the comfort of your own space.
When To Pursue Safety Training And Certification
In many industries, adhering to safety regulations is mandatory. Safety certifications and training ensure you remain updated with the latest industry standards and best practices. Also, staying on top of compliance requirements is critical to avoid penalties and ensure the safety of your workforce.
Furthermore, investing in safety training and certification can be a stepping stone to career advancement. It sets you apart from the competition and opens doors to higher-paying positions.
Invest In Your Safety Career
Investing in safety training and certification is an investment in your future and the well-being of those around you. Choose Coggno and gain access to a vast selection of safety courses, accredited certificates, and the convenience of online learning.